Maintcare » Knowhow » Instandhaltung / Instandhaltungscontrolling

Condition Monitoring
Inhaltsverzeichnis
Was ist Condition Monitoring?
Mit Condition Monitoring (Zustandsüberwachung) wird der technische Zustand einer Maschine mithilfe von Sensoren erfasst. Aussagekräftige Messwerte können hier Schwingungen, Vibrationen, Temperatur und Feuchtigkeit sein. Mit den gesammelten Daten können die Ist- und Soll-Werte einer Maschine verglichen werden. So lassen sich Materialermüdung und Fehler der Maschine für entgegenwirkende Maßnahmen frühzeitig erkennen. Mit CM wissen Sie, was wann passiert und lernen Ihre Maschinen besser zu verstehen.
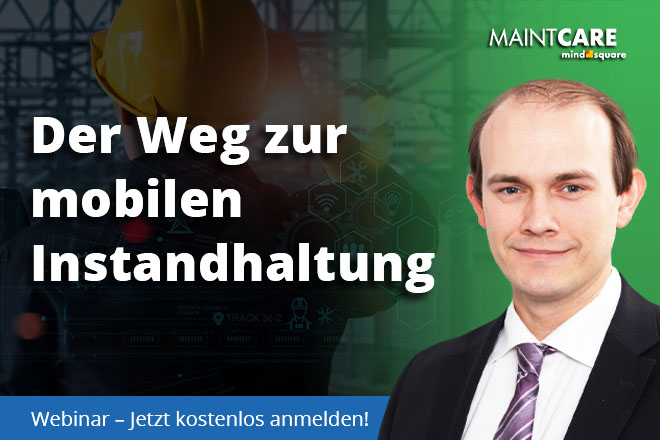
Ziele
Die Zustandsüberwachung verfolgt im Wesentlichen 2 Ziele:
- Maschineneffizienz bei maximaler Auslastung durch die frühzeitige Erkennung von Materialermüdung und
- Sicherheit für den Menschen, da durch die Fehlerfrüherkennung ein schnell reagierendes Alarmsystem, z. B. eine Notfallabschaltung, integriert werden kann.
Strategie
Es gibt 3 Arten von Instandhaltungen. CM gehört zur zustandsorientierten Instandhaltung und steht somit zwischen reaktiver und präventiver Instandhaltung. Während die reaktive Instandhaltung nur dann durchgeführt wird, wenn eine Maschine tatsächlich ausgefallen und gewartet werden muss, werden bei der präventiven Instandhaltung mitunter noch funktionstüchtige Teile ausgetauscht. CM gleicht die Schwächen der beiden Varianten aus. Die Analyse der Messwerte macht Fehler rechtzeitig erkennbar, bevor es zu einem Produktionsstillstand kommt. Durch die mögliche Analyse der Ursache wird die Lebensdauer der Maschinenteile voll ausgekostet.
Anwendungsgebiete
Condition Monitoring ist insbesondere an rotierenden Anlagen, Elektro- und Verbrennungsmotoren, Kompressoren, Pumpen und in der Prozesstechnik zu finden.
Wie funktioniert Condition Monitoring?
Teilschritte
Die Zustandsüberwachung lässt sich in 3 Teilschritte gliedern, wobei Punkt 1 und 2 vorwiegend der Instandhaltung nach DIN 31051 entsprechen:
- Die Zustandserfassung meint die Messung und Dokumentation der physikalischen Werte mittels Sensoren.
- Der Zustandsvergleich ist die Gegenüberstellung von Ist- und Soll- bzw. Grenzwerten der Maschinen.
- Die Diagnose analysiert und lokalisiert aus der Gegenüberstellung der Werte mögliche Fehler und ermöglicht somit frühzeitige Maßnahmen der Instandhaltung, die sinnvoll in den Produktionsplan integriert werden können.
Sensorik
Maschinen der Produktionsindustrie müssen an der Stelle mit Sensoren ausgestattet werden, wo relevante Messwerte für die Zustandsanalyse gewonnen werden können. Es gibt Maschinen mit bereits vorhandener Sensorik oder die Möglichkeit diese nachzurüsten.
Die Sensoren lassen sich in folgende Funktionen unterteilen:
- Schwingungsüberwachung an Antrieben kann an rotierenden Maschinen zur Überwachung von Achsen und Lager angewendet werden.
- Partikelüberwachung in Hydraulikflüssigkeiten erfasst die Schmierstoffzusammensetzung mithilfe von einem elektronischen Mikroskop.
- Wärmeüberwachung mittels Infrarot- oder Thermosensoren gibt Aufschluss über die Hitzeentwicklung einzelner Maschinenteile.
- Akustische Überwachung misst Signale im Hochfrequenz-Spektrum mithilfe digitaler Ultraschallgeräte und lokalisiert so Reibungen und Fehler an beweglichen Maschinenteilen.
- Ölstandüberwachung analysiert Verschmutzungen in der Ölzusammensetzung.
Messstrategien
Zeitraum
Die Überwachung der Maschine kann intermittierend, entweder in regelmäßigen oder variablen Intervallen, oder kontinuierlich in Echtzeit erfolgen. Die intermittierende Messung ist in der Lage eine langfriste Zustandsentwicklung der Lebensdauer aufzuzeigen, ist jedoch für kurzfristige Abweichungen nicht geeignet. Die kontinuierliche Messung kann lang- und kurzfristige Entwicklungen lückenlos dokumentieren.
Netzwerk
Die Daten können über ein verkabeltes oder drahtloses Netzwerk an das Monitoring-System weitergegeben werden. Das drahtlose Netzwerk ist in der Regel schneller umsetzbar, da keine Kabel verlegt werden müssen, jedoch auch anfälliger für Störungen durch externe Faktoren. Bei einem verkabelten Netzwerk muss ggf. die Schirmung der Kabel beachtet und E-Pläne aktualisiert werden.
Condition Monitoring System (CMS)
Das CMS umfasst die gesamte Kommunikationsstruktur von der Messung der Daten bis zu deren Visualisierung auf beliebigen Endgeräten. Die Sensoren geben die Messwerte an ein Monitoring-System weiter, welches an einen Router angeschlossen ist. Der Router leitet die Daten über das Internet an einen Server weiter, der diese dann an die Überwachungszentrale ausspielt. Hier können die Daten analysiert werden.
IoT-Lösungen bieten IoT-Gateways zum Sammeln und zur Aufbereitung der Messwerte an. Ein IoT-Hub (z. B. Microsoft Azure oder SAP Leonardo IoT) gibt die Werte aus und veranschaulicht die Ergebnisse für den Menschen.
Darüber hinaus können die Messdaten mit weiteren Parametern aus dem Prozessmanagement (Fertigungsprozess), dem Qualitätsmanagement (Schadensstatistik) sowie dem Gebäudemanagement (Sicherheitsmaßnahmen, Raumtemperaturen) zusammengeführt werden, um ein ganzheitliches Überwachungssystem zu erstellen.
Datenspeicherung Online vs. Offline
Hier stellt sich die Frage, wer von wo Zugriff auf die Daten benötigt. Reicht es aus, die Daten lokal (On-Premise) zu speichern oder ist die Verwendung einer Cloud für mobile Anwendungen sinnvoll? Wenn die erfassten Daten über das Internet für mobile Geräte verfügbar gemacht werden sollen, sind auch Datenschutz und Cybersicherheit zu bedenken.
Integration mithilfe von Lean Maintenance
Der Einsatz von CM muss nicht immer ganzheitlich und somit kostenintensiv erfolgen. Es gibt auch individuelle Einstiegsmöglichkeiten, die sich an internen Ressourcen orientieren und beispielsweise nur die höchsten Risikofaktoren überwachen, ohne die gesamte Infrastruktur ändern zu müssen. Gerade für kleinere Industrieunternehmen ist der flexible Einsatz der Zustandsüberwachung interessant. Die wichtigste Frage ist hier, welches Überwachungsziel erreicht werden soll. Das Prinzip von Lean Maintenance kann helfen eine zielgerichtete Überwachung zu finden. Es ermittelt, welche Instandhaltungsstrategie für einzelne Maschinen am sinnvollsten ist.
Im ersten Schritt werden Maschinen nach ihrer Wichtigkeit für den gesamten Wertstrom von der Kundenbestellung bis zur Auslieferung sortiert. Einige werden eher selten verwendet, andere wiederum beeinflussen die Produktion massiv. Würde eine Maschine sogenannte Engpässe im Wertstrom verursachen, wäre diese für die Zustandsüberwachung geeignet.
Da jede Maschine aus mehreren Anlagenteilen besteht, zielt der zweite Schritt darauf ab, die risikoreichsten Komponenten zu ermitteln. Die Fehlermöglichkeiten- und -einflussanalyse (FMEA) kann hier bei der Beurteilung helfen. So lassen sich auch geeignete Positionierungen für Messsensoren ermitteln. Es ist sinnvoll diesen Schritt nur bei den priorisierten Maschinen aus Schritt 1 anzuwenden.
Anschließend lassen sich die Maschinen in Schadklassen von 1–8 einteilen, die nach Auswirkung auf den Anlagenbetrieb (A), Schadenshäufigkeit (S) und Prognostizierbarkeit (P) definiert sind. Während die Schadklassen 1–4 als unkritisch betrachtet werden, sind die Schadklassen 5–8 für das Condition Monitoring geeignet. Eine Übersicht der Schadklassen finden Sie im Link der Bildquelle in Abb. 4.
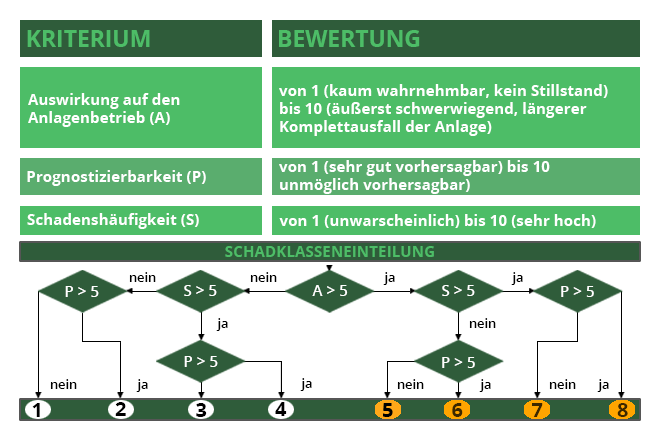
Abb. 4: Einteilung in Schadklassen nach Lean Maintenance. Quelle
Outsourcing
Die Auswertung der Messdaten durch Expert*innen ist grundsätzlich empfehlenswert, sofern das Know-How im eigenen Unternehmen nicht vorhanden ist. Ein komplettes Outsourcen der Zustandsüberwachung macht bei großen Produktionsanlagen Sinn, da je nach Komplexität das Auslesen der Daten immer schwieriger wird. CM-Anbieter erarbeiten mit Ihnen auf Basis Ihrer Ziele eine Überwachungsstrategie, helfen bei der Installation der Technik und unterstützen Sie auch bei der Instandhaltung und Ersatzteillieferung.
Vorteile und Herausforderungen
Das Potenzial der Zustandsüberwachung ist vielseitig und zukunftsorientiert. CM ist der Anschluss an die digitale, vernetzte Welt der Industrie 4.0. Themen wie Machine-Learning (M2M) und Industrial Internet of Things (IIot) sind Meilensteine zur Smart Factory. Die Umsetzung birgt einige Herausforderungen, die sich im Wesentlichen mit der Fragestellung, was, wann, wo, wie und womit überwacht werden soll, beschäftigt.
Vorteile
- Die Überwachung des Maschinenzustandes ermöglicht eine Prognose der Restlebensdauer.
- Systemabweichungen werden frühzeitig erkannt.
- Die Messwerte helfen bei der Ursachenfindung.
- Auf einen möglichen Maschinenstillstand lässt sich schneller reagieren.
- Betriebsausfälle können auf ein Minimum reduziert werden.
- Energiekosten, Wartung- und Instandhaltungskosten werden gesenkt.
- Die Maschinenleistung bzw. die Gesamtanlageneffektivität (OEE: Overall Equipment Efficiency) wird erhöht.
- Die Qualität der Prozessabläufe und Produkte wird optimiert.
- Instandhaltungsmaßnahmen lassen sich vorausschauend in den Produktionsplan integrieren.
- Die Arbeitssicherheit für Mitarbeiter*innen wird verbessert.
- Sicherheitsmaßnahmen lassen sich besser integrieren.
- Der Einsatzumfang lässt sich nach individuellen Bedürfnissen abstimmen.
Herausforderungen
- CM kann keine spontanen Ausfälle der Maschine erkennen, wie z. B. ein Gewaltbruch einer Antriebswelle
- Gerade für den kontinuierlichen Einsatz von CM müssen die Messdaten im Stil von Big Data verwaltet werden.
- Das Lesen, Verstehen und Deuten der Messdaten ist essentiell für die Wirksamkeit der Zustandsanalyse. Hier sind Expert*innen gefragt.
- Der Einsatzumfang muss nach individuellen Bedürfnissen an die Maschine gut überlegt werden. Fragen wie:
- Welche Messparameter sind aussagekräftig bzw. notwendig, um das gewünschte Ziel zu erreichen?
- Welche Anforderungen an die Zuverlässigkeit der Maschine sind notwendig und realistisch?
- Eine ganzheitliche Überwachung ist kostenintensiv, aber nicht immer notwendig.
- Datenschutz und Cybersicherheit müssen beachtet werden.
Condition Monitoring und Predicitive Maintenance
CM ist eine Voraussetzung für das Konzept von Predictive Maintenance (vorausschauende Instandhaltung). Das Ziel von PM ist es, den optimalen Zeitpunkt einer Wartung auf Basis berechneter Eintrittswahrscheinlichkeiten vorherzusagen, sodass nur gewartet werden muss, wenn es tatsächlich notwendig ist. Hierfür sind die in Echtzeit gemessenen Daten aus der kontinuierlichen Zustandsüberwachung essentiell. Um der Datenflut gerecht zu werden, muss das System um eine digitale, intelligente Kommunikationsstruktur erweitert werden. CM liefert also Daten für den Status Quo, während PM die Daten für eine Vorhersage der Zustandsentwicklung einer Maschine auswertet.
Fazit
Durch die Fehlerfrüherkennung des Condition Monitoring lassen sich Maschineneffizienz, Lebensdauer und der Produktionsprozess optimieren und Instandhaltungs- und Energiekosten senken. Sie lernen Ihre Maschine besser kennen, können rechtzeitig Ersatzteile bestellen und die Instandhaltung sinnvoll in die Produktion einplanen.
Dem gegenüber stehen die Kosten für die Überwachungstechnik und Integration eines CM-Systems. Jedoch ist eine permanente, vollumfängliche Überwachung nicht immer notwendig. Der Einsatz richtet sich nach individuellen Bedürfnissen und Überwachungszielen. Fakt ist, dass die Digitalisierung auch in der Instandhaltung 4.0 stetig voranschreitet.
Condition Monitoring bietet einen Einstieg dem Trend zu folgen und wettbewerbsfähig zu bleiben.
FAQ
Was ist Condition Monitoring?
Condition Monitoring, auch Zustandsüberwachung genannt, erfasst den technischen Zustand von Maschinen mithilfe von Sensoren. Dabei werden verschiedene Messwerte wie Schwingungen, Vibrationen, Temperatur und Feuchtigkeit erfasst, um den Ist-Zustand der Maschine zu überwachen und mit Soll-Werten zu vergleichen.
Welche Ziele verfolgt die Zustandsüberwachung?
Die Zustandsüberwachung hat zwei Hauptziele. Erstens die Maximierung der Maschineneffizienz bei maximaler Auslastung durch frühzeitige Erkennung von Materialermüdung und zweitens die Sicherheit für den Menschen durch Fehlerfrüherkennung und Integration eines schnell reagierenden Alarmsystems.
Wie funktioniert Condition Monitoring?
Das Condition Monitoring gliedert sich in drei Teilschritte: Zustandserfassung, Zustandsvergleich und Diagnose. Sensoren erfassen physikalische Werte, die dann mit Soll- oder Grenzwerten verglichen werden. Durch die Analyse der Messwerte können mögliche Fehler frühzeitig erkannt und geeignete Instandhaltungsmaßnahmen eingeleitet werden.
Wo findet Condition Monitoring Anwendung?
Unternehmen setzen das Condition Monitoring insbesondere bei rotierenden Anlagen, Elektro- und Verbrennungsmotoren, Kompressoren, Pumpen und in der Prozesstechnik ein.
Haben Sie weitere Fragen zum Condition Monitoring? Dann kommen Sie gerne auf uns zu.
Wer kann mir beim Thema Condition Monitoring helfen?
Wenn Sie Unterstützung zum Thema Condition Monitoring benötigen, stehen Ihnen die Experten von Maintcare, dem auf dieses Thema spezialisierten Team der mindsquare AG, zur Verfügung. Unsere Berater helfen Ihnen, Ihre Fragen zu beantworten, das passende Tool für Ihr Unternehmen zu finden und es optimal einzusetzen. Vereinbaren Sie gern ein unverbindliches Beratungsgespräch, um Ihre spezifischen Anforderungen zu besprechen.