
So optimieren Sie Ihre Instandhaltungsprozesse
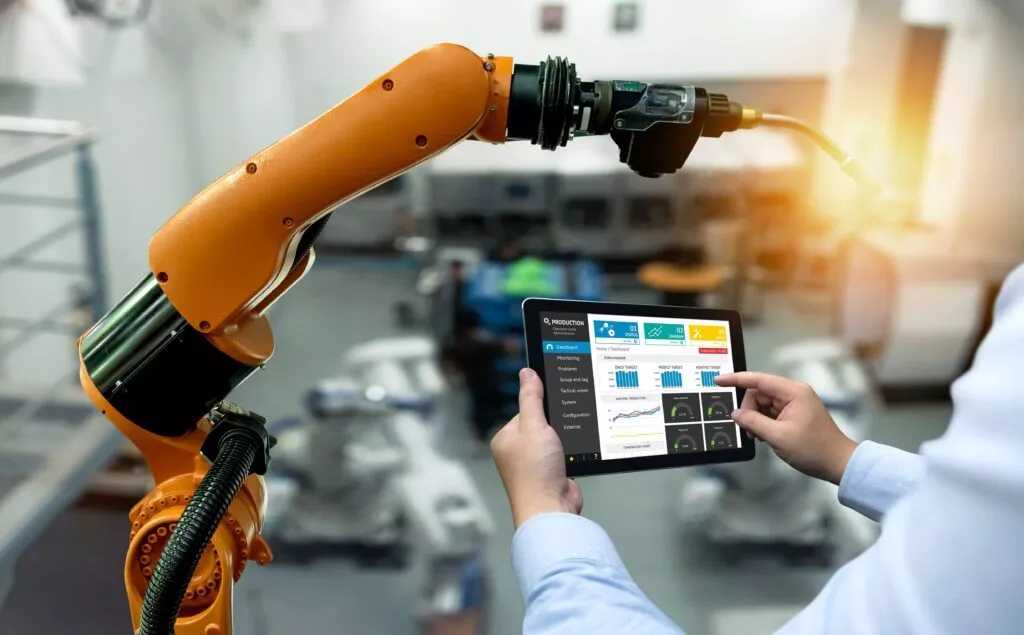
Unternehmen versuchen stets ihre Prozesse zu optimieren und somit Kosten zu reduzieren. Dabei stellt das Instandhaltungsmanagement großes Optimierungspotenzial dar. Wenn es bspw. zum Ausfall von Anlagen kommt, steigt der Aufwand der Instandhaltungsmaßnahmen. Wir zeigen Ihnen, wie Sie Ihre Instandhaltungsprozesse optimieren.
Wie Sie Ihre Instandhaltungsprozesse optimieren und sogar Probleme vorzeitig erkennen, zeige ich Ihnen in diesem Beitrag.
Was sind die Ziele einer optimalen Instandhaltung?
Eine suboptimale Instandhaltung nimmt nicht nur viel Zeit in Anspruch, auch die Kosten sind viel zu hoch. Auf der einen Seite kommt es zu unnötigen Wartungsarbeiten, da Anlagen eigentlich noch problemlos laufen. Auf der anderen Seite kommt es zu unerwarteten Stillständen, weil Verschleiße falsch eingeschätzt wurden.
Bei einer optimierten Instandhaltung sollen u. a. Produktionsstillstände vermieden werden, damit die Zuverlässigkeit der Anlage erhöht wird und Sie sich flexibel den Marktanforderungen anpassen können. Zudem soll auch die Produktionsleistung und die -qualität verbessert werden. Das größte Ziel, das eine optimierte Instandhaltung verfolgt, ist jedoch die Kostensenkung.
Wie Sie von einer Dokumentation der Instandhaltung profitieren
Zwar sind Unternehmen dazu verpflichtet, Wartungen und Instandhaltungen zu dokumentieren. Sie sollten das jedoch auch aus eigenem Interesse tun, da sich daraus viele Vorteile ergeben. Der Instandhalter ist mit einer gründlichen Dokumentation nämlich in der Lage, wichtige Zusammenhänge zwischen Prozessen zu erkennen und so Fehler zu entdecken und diese zu beseitigen. Außerdem kann die Dokumentation von anderen Mitarbeitern eingesehen und als Checkliste benutzt werden.
Sammeln Sie Informationen und Daten
Neben der Dokumentation der Instandhaltungen und Wartungen können Sie weitere Informationen sammeln, um Ihre Instandhaltungsarbeiten effektiver zu gestalten. Statten Sie Ihre Maschinen und Anlagen mit Sensoren aus, so dass Daten über alle Prozesse gesammelt werden können.
Von Temperaturdifferenzen, über Bestellzyklen von Ersatzteilen, bis hin zu Störgeräuschen – Sie können von einer Vielzahl an Informationen Gebrauch machen. Aus diesen Daten lassen sich nämlich Korrelationen ableiten, mit denen Sie Ihre Instandhaltungsprozesse optimieren können. Wenn bspw. die Luftdruckmesswerte sinken, gibt es Probleme mit der Hydraulik. Aus gesammelten Daten können Sie den Zustand Ihrer Anlage auslesen und so bei Störungen schneller reagieren.
Individuell an Ihre Bedürfnisse angepasst
Bei einer reaktiven Instandhaltung müssen Sie mit längeren Stillstandzeiten und den damit verbundenen Umsatzverlusten rechnen. Ungeplante Ausfälle und Störungen können Sie zwar nicht vollständig umgehen, jedoch können Sie diese mit regelmäßigen Instandhaltungen gering halten (geplante Instandhaltung). Dabei kann es eine allgemeine Zeitangabe für Wartungs- und Instandhaltungszyklen nicht geben – zu unterschiedlich sind Industrien, Maschinen und Anlagen sowie deren Nutzung und Abnutzung.
Für eine optimierte Instandhaltung brauchen Sie also ein an Ihr Unternehmen individuell angepasstes Instandhaltungsmanagement. Es existieren unterschiedliche Ansätze und Systeme, mit denen Sie Ihre Instandhaltungsprozesse optimieren können. Etabliert hat sich mittlerweile in vielen Unternehmen der ganzheitliche Ansatz des Total Productive Maintenance (TPM). Predictive Maintenance geht noch einen Schritt weiter.
Was ist Total Productive Maintenance (TPM)?
Unter Total Productive Maintenance (TPM) ist ein ganzheitliches Anlagenmanagement zu verstehen, bei der die Produktion und Instandhaltung gemeinsam agieren. Dadurch, dass das Produktionspersonal für die Instandhaltung verantwortlich ist, kann das Personal schneller auf Störungen reagieren und so Stillstandzeiten verkürzen. Die Grundlage von TPM bildet diese autonome Instandhaltung.
Das Ziel von TPM ist es, die Mitarbeiter so zu informieren und qualifizieren, dass sie autonom agieren können. Sie sind in der Lage, Schwachstellen strukturiert zu analysieren, damit diese dauerhaft beseitigt werden. So ist das Produktionspersonal Experten der Maschinen und Anlagen, an denen sie tagtäglich arbeiten.
Bei TPM wird die gesamte Anlage zielgerichtet und kontinuierlich verbessert, so dass einer produktionsfokussierten Instandhaltung nichts im Weg steht. Verluste und Verschwendung werden so gut wie möglich verhindert, indem der Fokus auf der Prävention liegt.
Vorausschauende Analysen mit Predictive Maintenance
Predictive Maintenance beschreibt eine vorausschauende Instandhaltung, die mithilfe von intelligenten Systemen Fehler an Anlagen erkennt, bevor diese überhaupt entstehen. Dafür sammeln die Sensoren unterschiedliche Daten wie Temperatur oder Störgeräusche, die analysiert werden und bei Abweichungen Alarm schlagen. Auf Basis digitaler Daten können Sie Prognosen ziehen und perfekt getimte Wartungen einen optimalen Anlagenzustand erreichen.
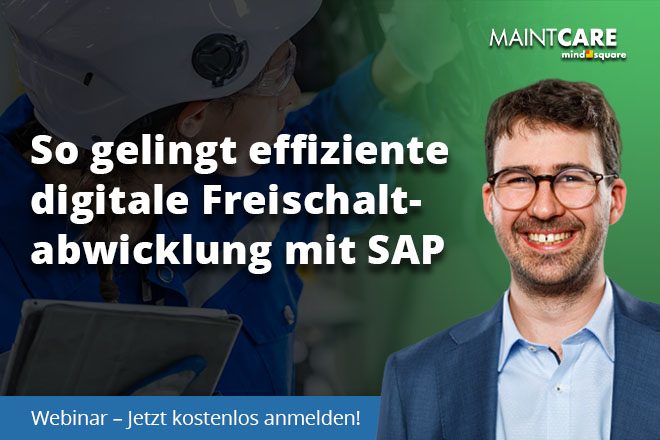
Dank SAP Predictive Maintenance werden Instandhaltungs- und Wartungsarbeiten nicht mehr turnusmäßig, sondern nach Bedarf eingesetzt, was zu einer Kostensenkung führt. Ungeplante Stopps transformieren sich durch eine zustandsbasierte Wartung planbar und vor allem viel kürzer.
Diese Vorteile bringen digitalisierte Instandhaltungsprozesse
Die Digitalisierung Ihrer Instandhaltungsprozesse bringt Ihnen viele Vorteile. Zum einen können Sie den Zustand der Anlage per App von überall einsehen. Zum anderen können Sie die Analysen dafür nutzen, optimale Zeiten für Wartungen und Instandhaltungen zu berechnen.
Außerdem können Sie Aufgaben mobil und digital verteilen, damit Instandhaltungsarbeiter von überall aus erreichbar sind. Bei Störungen wissen Sie direkt, wo sich der Instandhaltungsarbeiter befindet, der sich mit der Anlage am besten auskennt.
Bei einer Vorwarnung, dass ein Bestandteil bald ausgewechselt werden muss, können Ersatzteile rechtzeitig bestellt werden. So müssen die Teile durch die verbesserte Kontrolle und Planbarkeit nicht sicherheitshalber gelagert werden, wodurch Lagerplatz eingespart wird. Insgesamt können Sie mit vorausschauenden Analysen bis zu 30 % Wartungskosten einsparen und mit bis zu 70 % weniger Stillstandzeiten rechnen.
Digitale Instandhaltungsprozesse für Ihr Unternehmen
Instandhaltungsprozesse zu optimieren, birgt viel Potenzial. Indem Sie unterschiedliche Daten Ihrer Maschinen und Anlagen sammeln, können Sie Korrelationen zwischen Prozessen besser erkennen und so schneller die Ursache von Fehlern erkennen. Auch mit der Dokumentation der Instandhaltungsarbeiten verstehen Sie Zusammenhänge zwischen Prozesse besser. Mit einer digitalisierten Instandhaltung sind Sie u. a. in der Lage, von überall per App den Zustand Ihrer Anlage zu überwachen und den besten Zeitpunkt für die nächste Wartung zu berechnen.
Haben Sie weitere Fragen zu Optimierungen von Instandhaltungsprozessen? Dann kontaktieren Sie mich gerne.