Evolution der Instandhaltungsmethoden
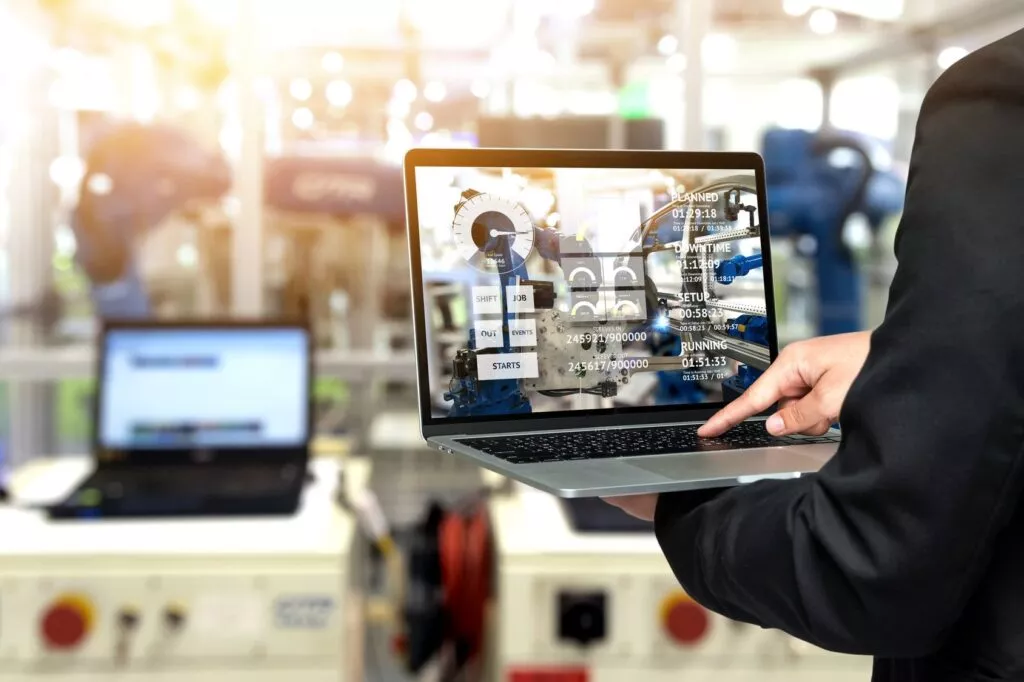
Um auf die Herausforderungen der Märkte und der Technik zu reagieren, haben Unternehmen ihre Strategien zur Instandhaltung weiterentwickelt. Die klassische, reaktive Instandhaltung wurde abgelöst: Statt die Reparatur einer Anlage nach einem Defekt in den Mittelpunkt zu rücken, sollte ein Ausfall im Vorfeld vermieden werden.
Preventive Maintenance
Die neuen Methoden wurden unter dem Schlagwort „Preventive Maintenance“ zusammengefasst. Die beiden wichtigsten Vorgehensweisen stellen wir hier vor:
Condition-based Maintenance
Bei der Condition-based Maintenance (zustandsabhängige Instandhaltung) werden Wartungsmaßnahmen ausgeführt, wenn eine Messgröße an einer Maschine einen bestimmten Wert erreicht hat. Voraussetzung hierfür sind regelmäßige Inspektionen, bei denen die Ergebnisse dokumentiert werden, oder automatisch erfasste Messgrößen.
Reliability-based Maintenance
Die Reliability-based Maintenance (Instandhaltung auf Basis der Zuverlässigkeit) basiert auf der Funktionsanalyse der Maschine. Im Anschluss werden Wartungsmaßnahmen, Bedienungsregeln und Anpassungen der Konstruktion einer Anlage abhängig von deren gewünschter Zuverlässigkeit definiert.
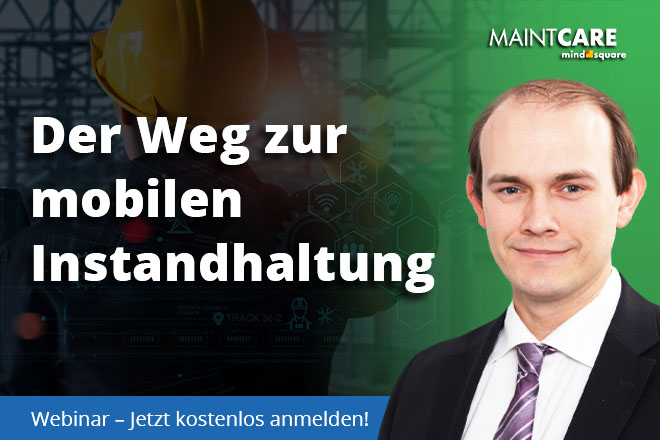
Predictive Maintenance
Sweet Spot zwischen präventiver und reaktiver Instandhaltung
Die Krux von Preventive Maintenance: Sie kann zum Kostentreiber werden, wenn Wartungen und Instandhaltungsmaßnahmen zu früh durchgeführt werden. Erfolgt die Wartung allerdings zu spät, ist der Schadensfall eingetreten und die reaktive Wartung kommt zum Einsatz. Damit sich die Investition rechnet und die Prozesse mithilfe von präventiver Instandhaltung optimiert werden, ist es entscheidend, den richtigen Zeitpunkt für die Wartung zu finden. Hier setzt die jüngste Instandhaltungsmethode an: Predictive Maintenance.
Vernetzung und KI ermöglichen optimalen Wartungszeitpunkt
Der Einzug von vernetzter Technologie und künstlicher Intelligenz in den Produktionsstraßen hat den Weg für vorausschauende Wartung geebnet. Sie lässt sich klar von der präventiven Instandhaltung abgrenzen. Denn sie geht einen entscheidenden Schritt weiter: Maschinen berechnen in diesem Fall selbst, wann der optimale Zeitpunkt für ihre Wartung gekommen ist – und setzen ihn nicht zu früh, sodass Investitionen in die Anlage optimal genutzt werden, und nicht zu spät, so dass die Funktion und Sicherheit jederzeit gegeben ist.
Um diesen perfekten Wartungszeitpunkt zu finden, werden Maschinen mit Sensoren sowie vernetzten Technologien ausgestattet und remote überwacht. Eine Vielzahl an Daten, zum Beispiel zum Verschleiß von Bauteilen, wird gesammelt und mithilfe geeigneter Software analysiert. Die Wartung wird nur ausgelöst, wenn ein Störfall wahrscheinlich ist.
Ausblick
Predictive Maintenance ist auf dem Weg, sich als neuer Standard in der Instandhaltung zu etablieren. Die neue Instandhaltungmethode ist verlässlicher und effizienter als ihre Vorgänger und bringt Unternehmen eine deutliche Kostensenkung, da sich ein Großteil der unerwarteten Ausfälle vermeiden lässt.
2 Kommentare zu "Evolution der Instandhaltungsmethoden"
Hallo Herr Lambertz,
wo sollte Ihrer Meinung nach der Schwerpunkt bei der Budgetierung der Instandhaltungsmethode liegen? In der Optimierung der Instandhaltungskosten oder in der Optimierung der Leistungsfähigkeit unserer Produktionsmaschinen?
Hallo,
ich würde mit der typischen Beraterantwort antworten “Es kommt darauf an”. Wenn Sie mehr produzieren/verkaufen könne und die Kostenseite noch nicht drückt, dann würde ich an der Optimierung der Leistungsfähigkeit arbeiten. Falls Sie jedoch das Gefühl haben das Sie durch Optimierung der Kostenstruktur ein erhebliches Einsparpotenzial haben, dann würde ich zu dieser Vorgehensweise raten. Sie können mich gerne kontaktieren um Ihren speziellen Fall zu besprechen.
Viele Grüße
Björn Lambertz